Scheuch LIGNO
Precision for clean production
Scheuch LIGNO GmbH is a Scheuch Group company and an international solution provider for clean air production with its headquarters in Mehrnbach, Austria. The company’s product range includes extraction technologies, surface technologies, mechanical and pneumatic conveying technologies, control technologies, disposal solutions and tested concepts for fire and explosion protection.
Since starting in the wood industry, Scheuch LIGNO has developed into a specialist for systems that are used in machining and processing of many different materials. This includes metal, paper, corrugated cardboard, insulants, plastics and rubber, composite materials, leather and textiles. Thanks to permanent innovation and further developments, Scheuch LIGNO is nowadays an important supplier of tailor-made solutions for healthy workplaces in many sectors with high dust emission intensity.
Scheuch LIGNO therefore always provides customers with the best and most cost-effective solution, regardless of whether they are an industrial business or a handicraft enterprise. The focus is always on increasing efficiency and reducing running costs. From consultation, project planning, production, logistics, assembly and commissioning all the way through to system servicing and emission measurements, Scheuch LIGNO provides a one-stop shop for every stage in the process.
Produced in austria
The entire Scheuch LIGNO product range is produced at the company headquarters in Mehrnbach, Upper Austria.
This includes the Scheuch LIGNO filter and pipe range, consisting of pipes, moulded parts and duct components. We use galvanized pipe material to ensure that our products are of the highest quality. A modern coil cutting system with integrated duct and pipe production rounds off the production facilities. Planning, programming and production of all switch cabinets and PLCs also takes place entirely in-house.
With a production surface area of around 4,260 m², a 280 m² cold hall and a 4,500 m² outdoor storage area, the company in Upper Austria has sufficient space for comprehensive production possibilities. This forms the basis of fast, flexible and high quality order processing.
Company history
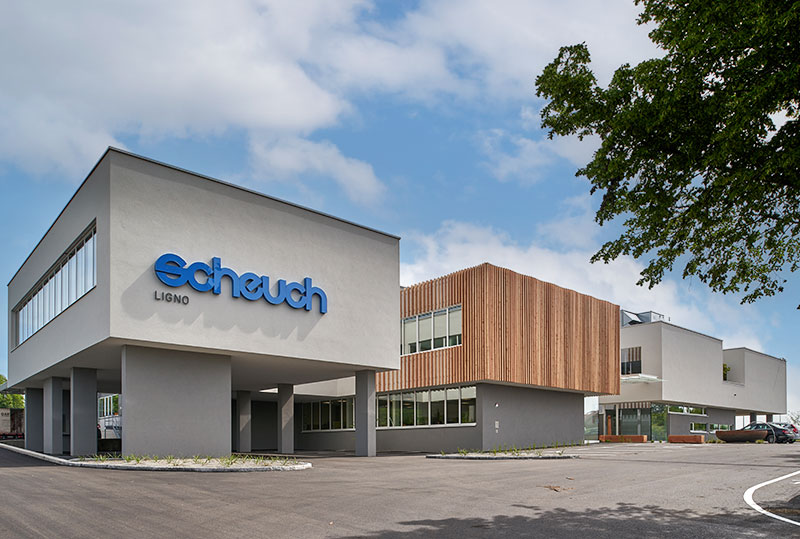
Scheuch LIGNO is based on 60 years of Scheuch history and experience in the wood industry. With the formation of the new Scheuch LIGNO GmbH business unit in 2015 from the Scheuch parent company, Scheuch LIGNO built its headquarters in Mehrnbach with an investment of eight million euro. Since then, the company has been writing a unique success story. The company output doubled along with the number of employees.
The range was expanded to other sectors, such as the metals industry recently. In Europe, Scheuch LIGNO GmbH is now one of the leading manufacturers of extraction, conveying, dedusting and flue-gas cleaning systems for the machining and processing industries for numerous materials.
To further boost this growth, we are continuously investing in expanding the Mehrnbach site, the last such investment was in 2021. A further branch in Germany supports our planning, project planning, installation and commissioning work in order to guarantee the brand promise of “The most cost-effective solution for industry and trade”.