Drying
Energy and cost-optimised solutions
After coating is before drying. To ensure that the material flow after painting continues at the required cycle time and the surface requirements are maintained, Scheuch LIGNO also plans the right paint drying. From the continuous dryer to the chamber dryer, the system components are adapted to the customer’s requirements. The coating components in combination with the coating system and the coating materials used have a significant impact on the drying principle required. Scheuch LIGNO designs the perfect paint dryer for your needs, be it an infrared dryer, convection dryer or jet dryer, all while taking energy optimisation and cost-efficiency into account continuously.
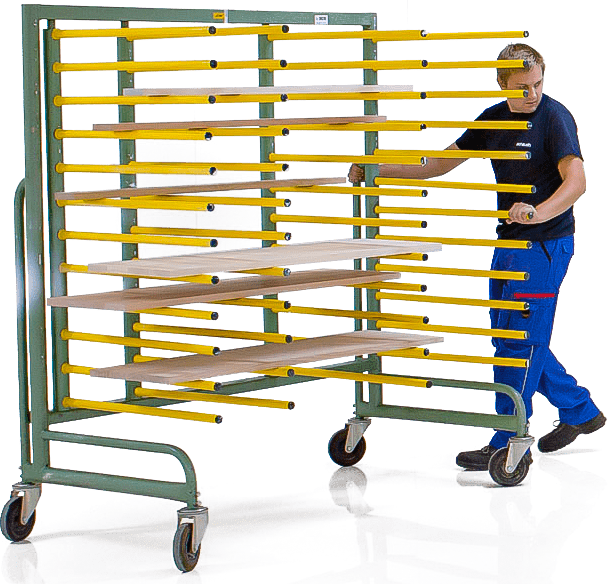
Booths for any requirement
Work processes and production steps must be meticulously planned and high quality requirements and standards must be met. Scheuch LIGNO has all the required expertise and will work with the customer to create the perfect environment for the painting system. Scheuch LIGNO pays attention to cost-effectiveness, employees, the environment and the applicable legal framework. And we create the perfect painting system for every customer’s needs.
Drying
With more exacting quality standards, but also due to the increased use of water-based paints, drying is often necessary in a separate room. The temperature, air volume, proportion of recirculating air and operating mode can be adapted precisely to the properties of the paint. In addition to drying in separate drying rooms, the selas+ system also allows a drying zone to be set up in the spray room. A proportion of the supply air or exhaust air is used to flash off the freshly painted parts in the storage area during painting. The air volume and run-down time can therefore be varied.
Drying rooms
With their ability to improve quality and shorten cycle times, drying rooms and drying booths are essential for modern coating processes. Scheuch LIGNO takes into account economic and ecological factors when building its drying systems and adapts the drying stage to the overall process. Depending on the coating in question, whether it involves water-based or solvent-based paints, the system is optimised with regard to temperature, humidity and air volume control. With more exacting quality standards, but also due to the increased use of water-based paints, drying rooms are necessary. The temperature, air volume, proportion of recirculating air and operating mode can be adjusted to suit the properties of the paint precisely.
Infrared dryers
Jet dryers
Jet dryers work by feeding hot air or gases that are sprayed onto the material to be dried in a specific pattern. This process cools the material’s surface effectively, causes moisture to evaporate and dries the material. Jet dryers are very versatile and used in various sectors. The jet dryer enables larger quantities of materials to be dried quickly and efficiently and can be adapted to the requirements of different materials.
Dryer ventilation technology
Extracted air is sucked through a supply air unit, pre-filtered and heated. The cleaned air can be guided through a heat recovery system if required. The heat recovery process reduces the operating and investment costs associated with the boiler unit that is being installed.
Minimising operating costs: Scheuch LIGNO extraction systems for surface coating can easily be equipped with heat recovery systems that reduce operating costs. Up to 85% efficiency, a variable rotor speed and operational monitoring ensure maximum heat recovery.