Wood chip silos
Storing materials in steel silos
The benefits of using steel silos as a material storage solution include the ability to assemble them quickly and easily, and their various sizes which allow them to meet all requirements.
Steel silos are predominantly used in eastern Europe and the CIS states for reasons relating to fire safety. Central Europe, on the other hand, mainly uses silos made of reinforced concrete.
Silo dischargers
When it comes to ensuring availability and operational safety in dedusting systems, discharge devices and conveying mechanisms are just as crucial as fans and filter systems. For decades, Scheuch has been producing rotary valves, screw conveyors, dosing devices and pendulum flaps in-house.
Extraction, filtration and material discharge devices thus form a single unit that consists of sophisticated and time-tested components. All conveying mechanisms are suitable for use in explosive, dust-laden atmospheres as defined in Directive 2014/34/EU (ATEX).
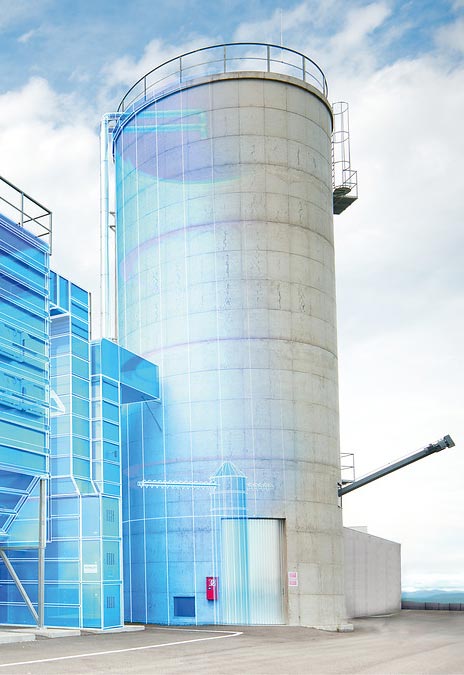
Horizontal silo discharger
The horizontal screw is the ideal discharge system for silo diameters of up to 10 metres. With its uncomplicated installation and low maintenance requirements, it is the number one choice for many satisfied customers in the craft and industrial sectors.
The horizontal discharger is installed in the centre of the silo. The screw uses forced feed to move horizontally across the silo floor around its own axis. It is possible to connect up to four screw conveyors or to feed several boilers and presses.
With many years of experience in silo technology, Scheuch LIGNO GmbH and LBH GmbH complement one another perfectly. The knowledge and expertise of both partners flow into the constant further development and optimisation of new, practical products for the wood sector.
Technical data:
Rotary valves
Rotary valves are used to discharge dust, chipboard shavings and fibrous conveyed goods, and as shut-off devices. A range of designs are available to suit various requirements, with throughput volumes to accommodate every case.
Scheuch rotary valves can also be delivered explosion pressure shock-resistant and type-tested ATEX-protective systems (ignition and flame penetration resistant) for explosion decoupling purposes.
Screw conveyors
Tube and trough screw conveyors are used to continually convey bulk materials at a volume flow area of 2 to 500 mg/h. Screw diameters are between 200 and 1,000 mm.
Silo explosion protection
Tried and tested safety
Many companies have silos which urgently need to be renovated from a safety point of view so that they meet all legal requirements. For existing silo systems, Scheuch LIGNO GmbH offers low-cost renovation solutions with which legal security can be guaranteed. When it comes to new silo systems, Scheuch LIGNO GmbH also always provides an economical solution that yields the very best performance.
In comparison to filter systems, silos have a much larger crude gas volume. The potential danger in the event of an explosion therefore increases accordingly: high pressure occurs, the flames reach up to 60 metres. Your own plot would be required for safe explosion protection. Scheuch demonstrates its solution expertise for this problem as well. Im more than 40 individual tests (under conditions similar to those in practice using wood dust), clear improvements could be demonstrated even if the Scheuch filling variants differed.
Maximum reliability through silo filling from scheuch ligno
The number of rupture discs can be reduced by 30 to 60 per cent according to the silo volume and filling method. It is therefore possible to fit a relief mechanism to the side for a particular purpose. Owing to the heavily reduced flame ranges and therefore the smaller hazard zones, additional surfaces then become available for operational use. The space required for new silo systems can therefore be reduced in the future. The practical tests performed by Scheuch LIGNO ensure that safety can also be proven.